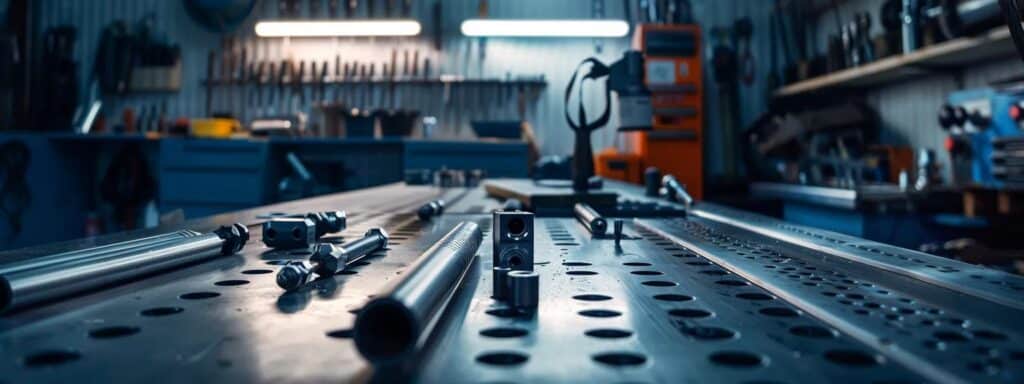
Quality Standards in Sheet Metal Fabrication: What Makes a Good Fabricator?
Sheet metal fabrication demands strict adherence to quality standards. Facilities managers seeking reliable metal fabrication services must understand both the technical details and the factors affecting production outcomes. High-quality fabrication ensures that products, from custom HVAC components to intricate architectural elements, meet rigorous specifications, leading to high customer satisfaction and fewer reworks. Modern fabricators in cities like Columbus, Ohio, integrate advanced technologies, expert craftsmanship, and continuous quality control to deliver superior parts manufacturing services.
In this article, The Sheet Metal Shop explains the key quality metrics, best practices, certifications, and technological enhancements that define good fabricators. Readers will learn which parameters to evaluate when choosing a metal fabricator and how challenges such as material variability and process defects are managed. Emphasis is placed on on-time delivery and customer satisfaction to help facilities managers make informed decisions for their custom fabrication needs.
Transitioning to the main content, each section below addresses critical factors and practices that ensure high-quality metal fabrication and answers common queries every responsible fabrication service provider should explain.
What Are the Key Quality Metrics in Sheet Metal Fabrication?
Quality in sheet metal fabrication is measured using metrics that ensure precision, durability, and consistency. Dimensional accuracy is verified by ensuring parts meet strict tolerance limits using calibrated equipment such as coordinate measuring machines (CMMs) and high-precision laser trackers. Surface finish is measured by quantitative roughness average (Ra) values to confirm the final product’s appearance and performance.
Material integrity is another essential metric. Proper heat treatment, sintering parameters for materials like carbon steel and aluminum, and fiber orientation in composites determine a part’s strength and reliability. Productivity metrics such as cycle time and yield percentages help assess process efficiency and economic viability. Standardized quality metrics, supported by Six Sigma and Lean Manufacturing principles, help reduce defects and waste while promoting continuous improvement. For instance, a defect rate below 1% compared with typical industry rates of 2–3% signals tight process control and customer reliability.
Which Precision and Accuracy Standards Define Quality Fabrication?
Precision and accuracy are maintained by adhering to prescribed tolerance levels and regular equipment calibration. Fabricators follow industry standards set by ANSI and ISO, using instruments such as micrometers, digital calipers, and laser measurement systems to achieve sub-millimeter precision. In high-end operations, such as aerospace parts manufacturing, tolerances can be as tight as ±0.005 inches. Automated machine tools and CNC systems further streamline production by programming repeatable cutting, bending, and welding operations. Statistical process control (SPC) is employed to ensure that every product falls within an acceptable quality distribution, reducing issues like misalignment or improper assembly.
How Do Material Selection and Handling Impact Fabrication Quality?
Selecting appropriate materials is as critical as the fabrication process itself. The intrinsic properties of materials, such as carbon steel’s strength, aluminum’s light weight, or bronze’s corrosion resistance, determine suitability for various applications, from interior design components to industrial brackets. Proper storage and handling techniques, including temperature control and correct stacking methods (FIFO), are used to minimize damage and maintain surface integrity. Advanced facilities use material tracking systems to record batch numbers, chemical composition, and heat treatment cycles. This precise compositional control is essential for applications demanding uniform mechanical properties. Additionally, training personnel in proper lifting, handling, and storage supports overall quality in production.
What Role Do Inspection and Testing Processes Play in Quality Assurance?
Inspection and testing are key to verifying that fabricated components meet design and safety standards. Quality control combines visual inspections with non-destructive testing (NDT) methods such as ultrasonic testing, radiographic inspection, and dye penetrant testing to detect concealed defects. A layered inspection process, beginning with raw material verification and extending through final product testing, ensures full traceability and accountability. Automated optical inspection systems using high-resolution cameras and machine learning further detect minor surface imperfections. Regular audits based on ISO 9001 or AS9100 standards support continuous process improvement and help prevent future defects.
What Best Practices Ensure High-Quality Metal Fabrication?
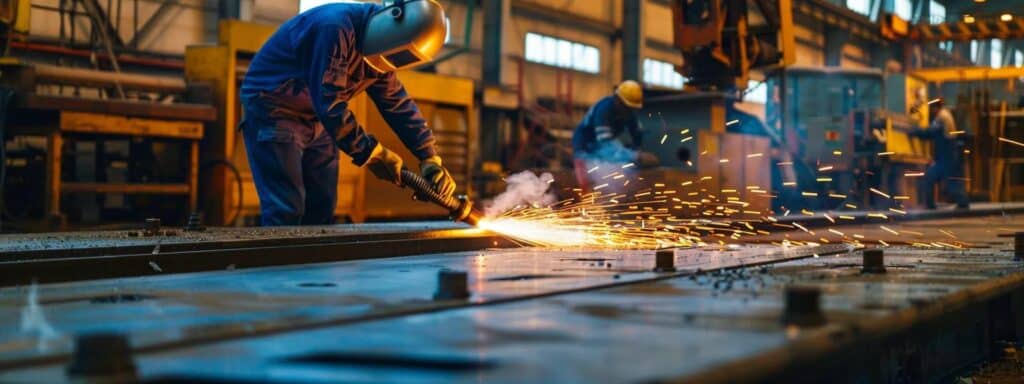
High-quality metal fabrication is accomplished through best practices that cover every production step, from design to delivery. Precision cutting using plasma or laser technologies minimizes heat distortion and creates sharp, clean edges ideal for applications such as automotive parts or machine tool components.
Workmanship in bending and forming operations is critical to maintain structural integrity. Using precise tooling adjustments, process simulations, and CAD software, operators can fine-tune bending to achieve the required curvature, even with challenging materials like stainless steel or exotic alloys. Similarly, welding and assembly are controlled via TIG or MIG welding processes monitored closely to avoid defects like porosity. Finishing techniques, such as polishing, coating, or painting, improve both aesthetic appeal and corrosion resistance, which is particularly important in industrial settings in Ohio.
How Are Cutting, Bending, Welding, and Finishing Optimized for Quality?
Optimization of these steps is achieved through strict process parameters and pre-established setups. Digital CNC plasma cutters and laser cutting machines are programmed to deliver consistently precise dimensions for complex geometries. Advanced press brakes in bending operations apply digital controls to keep angles within narrow tolerances. Automated systems in welding and post-weld heat treatments help prevent distortion, ensuring durable joints. Finishing processes like anodizing and powder coating further enhance the performance and longevity of the final product. Continuous training and data-driven process adjustments help maintain these optimized practices over time.
Why Is Customization and Flexibility Important in Quality Fabrication?
Customization enables fabricators to meet unique client requirements—from material properties to tailored design elements. In today’s competitive market, products may range from simple brackets to complex machine parts. Flexibility in fabrication allows process adaptations without compromising quality. Custom projects typically involve iterative feedback loops and prototyping, ensuring the final output meets client expectations whether for low-volume bespoke work or high-volume production. A robust digital infrastructure, including CAD/CAM software, supports swift modifications and enhances collaboration between engineers and fabricators, ultimately reducing lead times and increasing customer satisfaction.
How Does on-Time Delivery Affect Overall Fabrication Quality?
On-time delivery is essential for maintaining customer satisfaction and operational efficiency. Even when technical standards are met, delays can disrupt supply chains and project schedules. Reliable, timely delivery builds trust and reinforces a fabricator’s reputation. This is achieved through strategic planning, effective project management, and integrated production scheduling systems. Digital tracking and automated workflows ensure that every stage of the fabrication—from cutting to final assembly—proceeds on schedule. Robust contingency plans and inventory management further mitigate potential delays, ensuring projects remain on track.
Which Certifications and Standards Validate a Good Sheet Metal Fabricator?
Certifications and standards serve as external benchmarks that validate a fabricator’s adherence to high-quality manufacturing procedures. ISO 9001 is a widely recognized certification indicating commitment to systematic quality management and continuous improvement through documented processes and regular audits. In specialized markets like aerospace, AS9100 certification adds strict requirements for safety, reliability, and traceability. Other certifications, such as IATF 16949 for automotive components and NADCAP for aerospace and defense, further demonstrate a fabricator’s competence. These certifications assure customers that rigorous quality control measures are in place throughout the production cycle.
What Is ISO 9001 and Why Is It Important for Fabricators?
ISO 9001 outlines the criteria for an effective quality management system (QMS). Certification means that fabricators follow established procedures aimed at preventing errors, improving efficiency, and meeting customer requirements consistently. Rigorous audits and documentation reviews ensure that every production stage, from material handling to final assembly, is controlled. This framework builds trust with customers and regulatory bodies by enhancing internal processes, reducing waste, and ensuring predictable product performance.
How Does AS9100 Certification Benefit Aerospace Fabrication Quality?
AS9100, an extension of ISO 9001, addresses the stringent safety and quality requirements needed for aerospace components. It ensures that every fabrication step, from laser cutting to automated bending, is strictly controlled and monitored. The certification process requires extensive risk assessments and documentation, reducing the likelihood of defects in high-stress aerospace applications. For facilities managers in aerospace, AS9100 certification signifies superior process control, enhanced operational safety, and reliable, high-quality parts.
Are There Other Relevant Certifications to Consider?
Other certifications, such as IATF 16949 for automotive manufacturing and NADCAP for aerospace and defense, are also highly valuable. These standards, along with those set by bodies like ASME and local regulatory agencies, confirm that a fabricator maintains rigorous quality controls and consistent manufacturing practices. Verifying these certifications during the evaluation process ensures that potential fabrication partners are fully prepared to meet diverse and complex production demands.
How Can You Evaluate and Choose the Right Metal Fabricator?

Choosing a metal fabricator involves assessing quality indicators, certification credentials, and service reliability. Facilities managers should start by asking targeted questions about process capabilities, past project performance, and defect management strategies. Client testimonials, reference checks, and facility tours provide direct insights into a fabricator’s operational standards and quality assurance practices.
Digital platforms that track delivery times, customer feedback, and defect rates can supplement the evaluation. The ideal fabricator combines technical proficiency with excellent customer service, consistently managing material variability and delivering high-quality, on-time products.
What Questions Should You Ask Potential Fabricators?
When evaluating potential partners, ask: • Which certifications do you hold, and can you provide recent audit reports? • How is material variability managed during production? • What processes are in place to handle defects and rework? • What are your typical lead times and on-time delivery performance? • Can you provide documented evidence or case studies of past projects?
These questions help ensure that the fabricator has robust quality management systems and can accommodate scalable and custom production needs.
How Do Experience and Expertise Influence Fabrication Quality?
Years of experience and proven expertise are essential for consistent quality. Fabricators with a long track record bring skilled engineers and technicians who can anticipate production challenges and innovate processes. Their portfolios and client testimonials serve as proof of their capability to manage complex projects, whether involving intricate aerospace components or large-scale automotive parts. Continuous training and investment in advanced equipment like CNC machining and laser cutting further enhance quality and reduce production risks.
What Role Does Customer Satisfaction and References Play?
Customer satisfaction is a powerful indicator of a fabricator’s quality. Positive testimonials, repeat business, and long-term contracts demonstrate effective process control and reliable service. Facilities managers should review independent customer feedback and request references to gauge on-time delivery, defect rates, and post-production support. High satisfaction levels reflect a fabricator’s commitment to excellence and effective communication throughout the production process.
How Do Industry Applications Influence Quality Standards in Fabrication?
Different industries impose unique quality requirements on fabricated products. Aerospace fabrication, for instance, demands extremely tight tolerances and high-strength materials to ensure safety, while automotive fabrication requires both aesthetic quality and structural performance. In construction, durability and corrosion resistance are critical for products used in roofing, facades, and structural frameworks.
By aligning manufacturing processes with industry-specific standards, such as AS9100 for aerospace or IATF 16949 for automotive, fabricators ensure that their components integrate seamlessly into larger systems. This alignment, supported by regular audits and process calibrations, builds long-term trust and enhances overall performance.
What Are the Quality Requirements for Aerospace Sheet Metal Fabrication?
Aerospace fabrication requires precision with tolerances measured in fractions of a millimeter. Advanced inspection techniques like ultrasonic testing and digital metrology detect even minor defects, while detailed documentation ensures full traceability from raw material to finished component. The use of specialized materials such as high-strength aluminum or titanium alloys, processed under controlled conditions, further supports the stringent quality standards needed in aerospace. AS9100 certification assures that every process is rigorously monitored and controlled, delivering reliable components that meet safety and performance requirements.
How Does Automotive Fabrication Demand Affect Quality Metrics?
The automotive industry requires components that exhibit both high precision and durability. Fabricators must maintain strict tolerances and ensure consistent surface finishes while achieving the necessary mechanical strength and flexibility. Extensive testing, from impact resistance to vibration analysis, ensures that each part performs reliably under varied conditions. Advances in processes like spot welding and laser cutting help reduce weight without sacrificing strength, contributing to energy conservation and overall vehicle efficiency. Continuous real-time monitoring and data analytics refine quality metrics to meet these demanding standards.
What Quality Challenges Exist in Construction Metal Fabrication?
Construction applications pose unique challenges due to diverse environmental conditions. Fabricated components must resist weather fluctuations, corrosion, and other outdoor stressors. This makes material selection and protective finishing, such as powder coating or electropolishing, critical. Construction projects also require high precision to ensure that prefabricated parts integrate perfectly with other building elements. Continuous process improvements, automated quality control systems, and strict adherence to ASTM or local building standards all help mitigate these challenges and ensure long-term structural safety.
What Are Common Challenges in Maintaining Quality Standards?
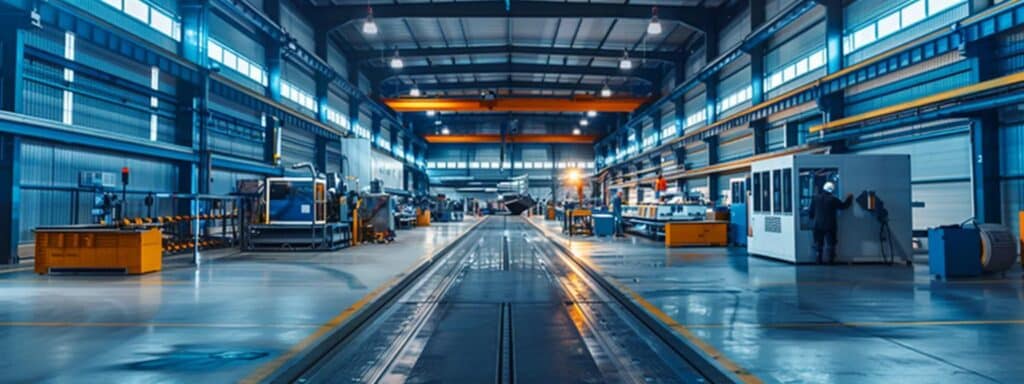
Maintaining quality standards throughout sheet metal fabrication involves overcoming challenges such as defects, rework, and material variability. Even slight deviations in the manufacturing process can lead to defects, causing costly rework and production delays. Strict quality control inspections, real-time monitoring, and effective feedback loops are essential in identifying issues early.
Material variability, such as differences in carbon content in steel or impurities in alloys, can adversely affect performance. Fabricators mitigate these risks through rigorous incoming inspections and supplier audits, ensuring that only materials meeting exact specifications are used. Continuous improvement initiatives, often based on Lean and Six Sigma methodologies, further reduce defect rates and enhance process reliability.
How Do Fabricators Manage Defects and Rework?
Fabricators manage defects by implementing a structured quality management system that emphasizes both prevention and correction. Real-time monitoring, statistical process control (SPC), and automated optical inspections help detect defects early. Root cause analysis is performed to understand and correct production issues, while thorough documentation of defects informs continuous improvement strategies.
What Impact Does Material Variability Have on Fabrication Quality?
Variability in raw materials can lead to inconsistencies in hardness, composition, and surface finish, affecting the integrity and performance of the final product. By enforcing strict material inspection protocols and conducting regular chemical and mechanical tests, fabricators ensure that only materials meeting precise specifications are used. This reduces defects and minimizes the need for rework, protecting customer trust and maintaining production efficiency.
How Is Continuous Improvement Implemented in Fabrication Processes?
Continuous improvement is achieved by employing methodologies such as Lean Manufacturing and Six Sigma. Regular process audits, employee training, and performance reviews identify areas for optimization. Data from quality inspections is used to adjust production parameters, while investments in advanced technologies, like automation and digital twins, help minimize process variations. This commitment to ongoing refinements drives productivity and enhances the overall quality of fabricated parts.
How Does Technology Enhance Quality in Sheet Metal Fabrication?
Technological advancements have revolutionized sheet metal fabrication by enhancing both quality and efficiency. Innovations such as CNC machining, advanced robotics, and digital design tools (CAD/CAM) allow for highly precise and consistent production, significantly reducing human error. Automation in cutting, welding, and finishing processes minimizes variability and defects, ensuring uniform output.
Digital design and prototyping enable engineers to simulate production conditions before manufacturing, identifying potential issues early. Advanced inspection techniques, including non-destructive testing (NDT) and in-line metrology systems, verify that each component meets design specifications. These technologies create a continuous feedback loop, driving improvements and providing fabricators with a competitive edge in meeting exacting standards.
What Role Do Advanced Cutting and Welding Technologies Play?
Advanced cutting methods, such as laser and plasma cutting, ensure high precision and clean edges by using computer-controlled systems that adhere to tight tolerances. These techniques reduce heat distortion and enable the production of complex designs that may be impossible with manual methods. In welding, automated systems and robotic arms consistently produce strong, defect-free joints. By minimizing rework and production downtime, these technologies boost overall output and product quality.
How Does Digital Design and Prototyping Improve Quality?
Digital design tools allow for detailed modeling and simulation of fabrication processes, helping engineers identify potential design flaws before manufacturing begins. Rapid prototyping through 3D printing or virtual simulations permits early testing and iterative improvements. This proactive approach reduces material waste, shortens turnaround times, and leads to smoother fabrication processes with a higher yield of conforming products.
Can Automation Ensure Consistent Quality in High-Volume Production?
Automation is key to achieving consistent quality in high-volume production. CNC machines and robotic assembly systems operate with high repeatability and precision, executing tasks with minimal human intervention. Sensors and real-time monitoring systems provide continuous feedback, allowing immediate adjustments to maintain tight tolerances and uniform quality. As production scales up, these automated processes become even more critical in ensuring that every component meets stringent quality standards.
Frequently Asked Questions
Q: What are the primary quality metrics in sheet metal fabrication? A: They include dimensional accuracy, surface finish, material integrity, and productivity metrics, measured using tools like CMMs, laser trackers, and micrometers. Sheet metal services include these metrics.
Q: How do certifications like ISO 9001 and AS9100 improve fabrication quality? A: They establish standardized quality management systems, ensuring continuous improvement, robust quality control, and adherence to industry-specific standards.
Q: Why is digital design important in improving fabrication processes? A: Digital design via CAD/CAM enables precise modeling, early flaw detection, reduced waste, and streamlined production workflows.
Q: How does automation contribute to maintaining quality in large-scale fabrication? A: Automation ensures uniform execution of tasks with CNC machines and robotic arms, reducing human error and ensuring consistent quality across high-volume production.
Q: What role do inspection and testing play in ensuring fabrication quality? A: They identify defects through methods like NDT and SPC, verifying that each component meets required specifications before final release.
Q: How should facilities managers evaluate potential fabricators? A: By asking detailed questions about certifications, process controls, past project experience, reviewing audit reports, and checking customer references.
Q: Can advanced technologies like laser cutting and automated welding really make a difference? A: Yes, these technologies ensure high precision and repeatability, substantially reducing defects and enhancing overall fabrication efficiency and quality.
Final Thoughts
The quality of sheet metal fabrication is driven by precise metrics, industry certifications, and advanced technological practices. Fabricators that integrate thorough inspection, digital design, automation, and continuous improvement processes deliver products that consistently meet high standards. Facilities managers are advised to prioritize partners with proven expertise, exceptional customer satisfaction, and robust quality management systems. Choosing a fabricator that effectively blends traditional craftsmanship with modern innovation is key to long-term success and operational excellence.